Manufacturing 4.0: A Look at the Bio/Pharma Industry
Manufacturing 4.0 is used to denote “smart factories” with increased levels of digitalization and automation. Where does the bio/pharma industry stand?
FDA study: Digital transformation for medical-product manufacturing
Manufacturing 4.0, referring to the fourth industrial revolution, involves creating so-called “smart factories” using advanced manufacturing technologies, digitalization, and increased automation. These features are common to a Manufacturing 4.0 approach in all industries with specific uses adopted for specific industries. This level of digital transformation is important not only in bio/pharmaceutical companies’ internal manufacturing networks but also in their external manufacturing networks through CMDO/CMOs.
To gain a perspective on both the opportunities and challenges in moving to a more digitalized and automated manufacturing environment, the US Food and Drug Administration (FDA) funded a study to analyze the advantages and barriers of smart manufacturing for medical products. The agency wanted to better understand the dynamics and conditions that impact a manufacturer’s decision and subsequent strategy to invest in and adopt digital technologies in their production by illuminating both perceived and demonstrated barriers from technical, business, and regulatory perspectives, and related cybersecurity considerations. The FDA was interested in this perspective not only for its overall understanding, but particularly for evaluating US responsiveness in light of the COVID-19 pandemic, which exposed gaps in the US manufacturing supply chain and the need to adopt and accelerate the implementation of digital technologies to improve supply-chain resilience, reduce time to market, or increase manufacturing capacity for medical diagnostics, therapies, and vaccines.
The study was conducted by MxD (Manufacturing x Digital), a national digital manufacturing institute that is partnered with the US Department of Defense, and the International Academy of Automation Engineering, an internationally recognized certification program. The project team evaluated nine manufacturers, involving 31 participants from US-based manufacturing sites. While the sample size of manufacturers was limited, most sites were represented by several participants, the majority in director level roles. Each participant completed a survey and two separate interviews with the project team. Of the 31 participants, 15 were from medical device/diagnostic manufacturing sites, eight from therapy-/drug-manufacturing sites, and four each from vaccine-manufacturing sites and personal-protective- equipment-manufacturing sites. The study was conducted between February and June 2021.
The project team used the BioPhorum Digital Plant Maturity Model as a basis for the assessment, which enables an assessment of a plant against five maturity levels (pre-digital plant, digital silos, connected plant, predictive plant, and adaptive plant) to provide a neutral assessment of the current state and to facilitate a discussion on a desired future state.
Key findings: Factors that hinder digital transformation.
Respondents were asked to rank in priority from top to bottom the factors that, in their opinion, most hinder digital transformation at their sites (see Figure 1). The most cited barrier was a manufacturer’s legacy systems, followed by insufficient internal funding, competing priorities of senior executives, organizational silos, and a lack of specific skills and talent. Other factors cited were conflicting corporate strategies, business technology (including IT) and business misalignment, regulation and compliance challenges, cybersecurity and privacy requirements, regulation and compliance challenges, a risk-adverse culture, and a lack of change-management best practices (see Figure 1).
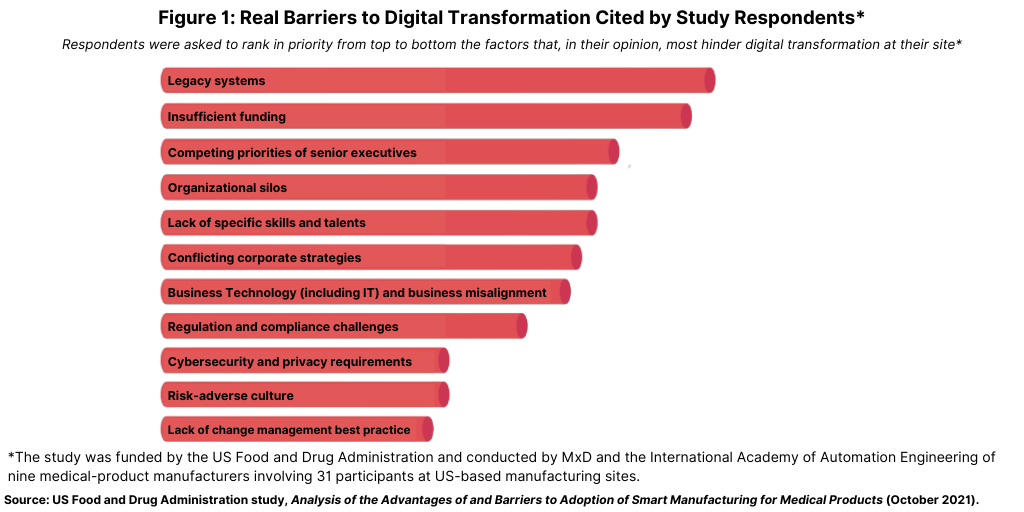
Key findings: Perceived barriers to digital transformation
The study also found that manufacturers perceived several barriers to realizing a goal of greater digitalization and automation in their operations. These perceived barriers are outlined below.
Misunderstanding that operational excellence is sufficient. A misunderstanding exists that a corporate approach to operational excellence is sufficient and does not need to be complemented by best practices and expertise from the disciplines of change management and human performance.
The technology gap is sometimes a psychological one. A lack of understanding of technologies or the inability of experts to adequately explain technologies can cause individuals to be more reluctant to adopt/trust new technology. Whether this is a real or perceived barrier, it is most likely person- and culture-dependent and may be reduced with education, training, and skills.
The perception that regulation may be a limitation. Engagement with regulators and internally within a company that present the value of proposed changes can mitigate the perception that regulation creates a barrier to implementation and change.
That new expertise depends on the infusion of talent through new hires. Capability-building through technical training and educational programs empowers internal talent. In a labor market that is already not producing enough talent to hire, this perceived barrier could be detrimental to the long-term success of the organization and lead to challenges with talent retention.
Key findings: Levels of digital mastery and transformation
The study evaluated survey respondents’ levels of digital transformation and based on those responses, placed them in one of four main categories: (1) Beginners; (2) Tech Wanders; (3) Conservatives; and (4) Digital Masters. Figure 2 shows the placement of respondents in these four main categories in a quadrant showing the respective level of digital transformation of the manufacturers participating in the FDA study.
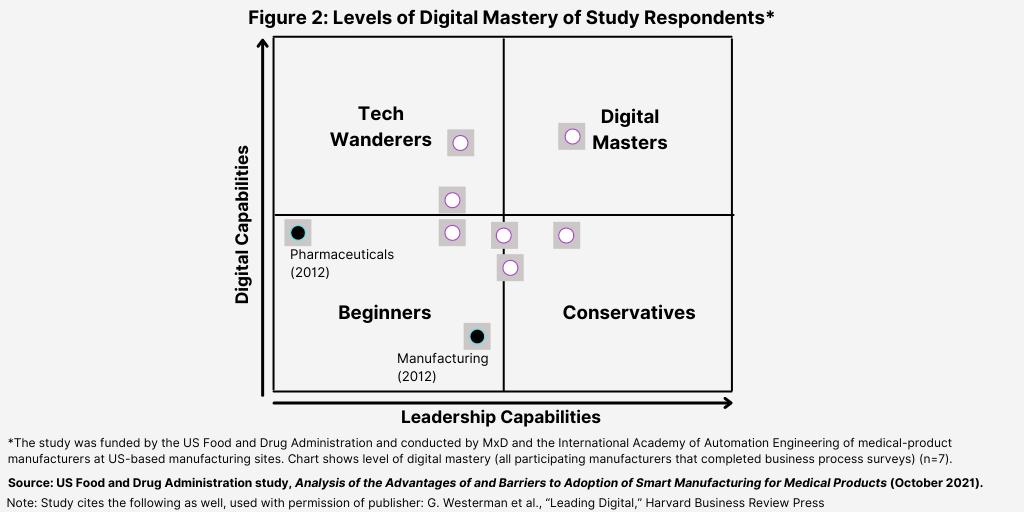
The levels of digital mastery of pharmaceutical manufacturers were found to have broadly improved when compared to a similar assessment done a few years ago that had placed the pharmaceutical industry in the Beginners quadrant. Such progress, according to the FDA study, is likely due to the emphasis placed on digital transformation in recent years and likely further accelerated by the pandemic.
For purposes of the analysis, Beginners are characterized by the following: (1) management skeptical of the business value of advanced digital technologies; (2) may be carrying out some experiments; and (3) immature digital culture. Tech Wanderers are characterized by the following: (1) many advanced digital features in silos; (2) no overarching vision; (3) underdeveloped coordination; and (4) digital culture may exist in silos. Conservatives are characterized by the following: (1) overarching digital vision, but may be underdeveloped; (2) few advanced digital features although traditional digital capabilities may be mature; (3) strong digital governance across silos; and (4) active steps to build digital skills and culture.
Digital Masters are characterized by the following: (1) strong overarching digital vision; (2) excellent governance across silos; (3) many digital initiatives generating business value in measurable ways; and (4) strong digital culture.
A deeper look shows where the nine manufacturers participating in the FDA study assess their companies’ standing in terms of digital transformation for manufacturing (see Figure 3). The overall picture shows that the majority of manufacturers assessed are only starting to emerge into digital activities, characterized first by having islands of automation (Level 2) and then a connected plant with a high level of automation, integration, and systems standardization (Level 3).
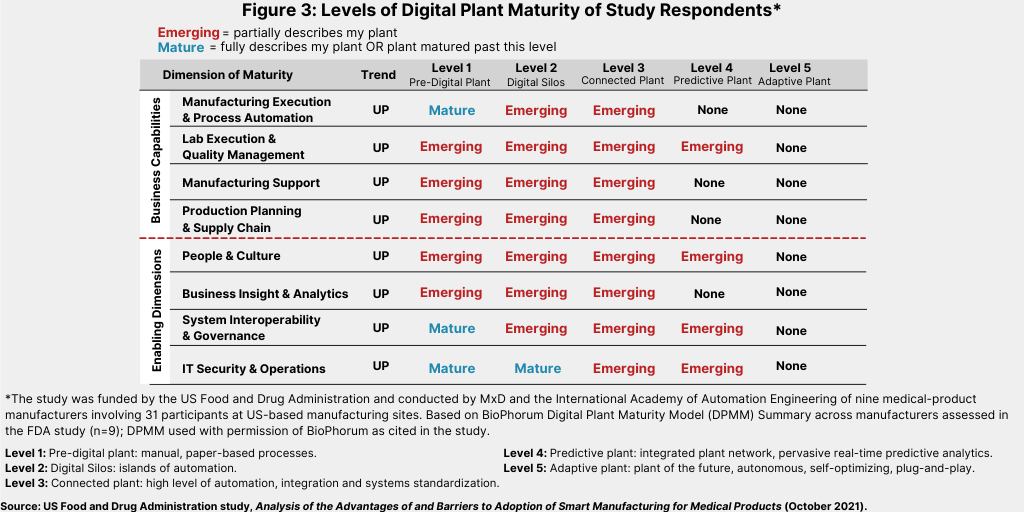
The study showed that not a single manufacturer surveyed, several of which had quite high levels of digital maturity, had a strong score in all the areas seen to be necessary for comprehensive digital transformation. Some sites have fully embraced and implemented new technologies, such as cloud computing, artificial reality/virtual reality, and robotic process automation, and many manufacturers have very mature digital transformation programs that have existed for more than 15 years. However, the overall picture is that the majority of manufacturers assessed are only starting to emerge into levels of digital transformation, and many are still highly reliant on paper-centric processes.